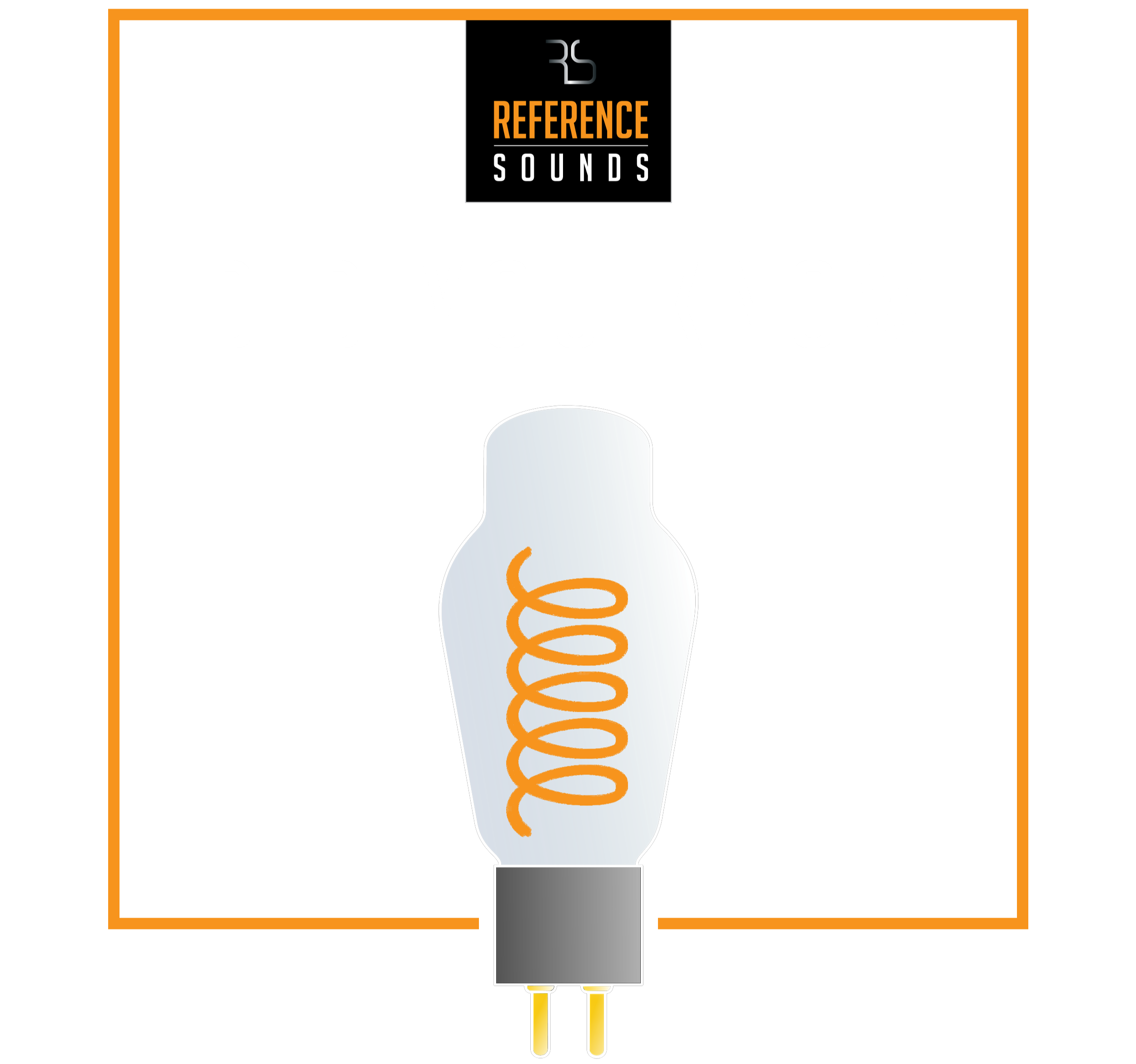
Reference Sounds Did You Know: geinige weetjes, interessante achtergronden en leuke tips over onze merken, producten, over ons en onze projecten.
Compressie Drivers
We have already seen a lot of children looking disappointed. Searching in vain with greasy fingers for the shiny dome of the tweeter and then lovingly pressing it into a greasy porridge. The engineers at JBL have raised a horn for this. Not necessarily because they dislike children’s fingers, but because of a deep-rooted belief in using the compression driver plus horn as the optimum reproduction of the treble. But what is actually behind that melted mailbox-looking horn and why is JBL so crazy about it. We tell you all about it in this new Did You Know.
Actually, this story starts deep in the last century. Somewhere around 1927, motivated by the introduction of sound film, a filmmaker decides that it is high time to provide films with dialogue and sound. Until then, the movies were silent. Accompanied at most by a sparse piece of piano playing or a guy with a piece of wood, stalling on stage when Charlie Chaplin hit the door with his gaff again. The music on the sound film was synchronized with the reproduction of the film and of course had to be reproduced in such a way that it could fill the entire room. Electric Watts were scarce, so the speaker used must be efficient and project the sound aimed at the audience. James B. Lansing was an absolute pioneer in loudspeaker technology and developed a unique compression driver horn combination especially for this application. In 1939, the MGM Theater equipped with Lansing’s Shearer Horn System won an Academy Award for Best Sound. He laid the foundation for Cinema and Live sound as we know it today and eventually started his commercial company in 1946. James B. Lansing Sound. JBL.
Efficiency and control over the radiating behavior are therefore the main ingredients of JBL’s compression driver horn combinations. But how? The vast majority of speakers are equipped with a ‘normal’ dome tweeter. Usually about 25mm in diameter, coming in the most exotic types of material and super attractive to press. This direct-radiating driver is a proven concept and speaker builders build fantastic speakers with it. However, this technique – like any other – has its challenges. First of all, the transition from the small dome to the large surrounding air volume creates an extremely inefficient coupling. It’s exactly why the parents on the sidelines of the hockey field curl their hands around their mouths when they shout at their Wouterrrr.
The acoustic mismatch from tweeter dome to air due to the acoustic radiation impedance means that only a very small part of the electrical input signal is converted into sound. Only about 2 to 5%. The rest has to put up with the poor tweeter in its voice coil with increasing distortion and risk of overload as a result. In addition, the energy yield of the tweeter is very dependent on the angle at which you hear it and, moreover, very frequency dependent. Right in front of the speaker, its sound output is super tight, but next to the axis of the speaker, the output collapses like a pudding. The result is a relatively small spot where the speaker projects its energy in optimal sound balance – the sweet spot. Not ideal if you want to enjoy a movie or piece of music with the entire hockey team.
This is exactly why James developed the first Compression Driver horn combination in 1927. With numerous patents, JBL is lord and master of this technique. An artful interplay between driver and horn, transition from high to low acoustic radiation impedance and the targeted projection of energy into the room. It starts with the driver. Instead of coupling directly to the air as with a standard tweeter, JBL couples the diaphragm to a small chamber – the compression chamber. The accumulated energy can then leave the compression chamber through a phase plug with small openings. Due to this special construction, the sound pressure increases, a bit like squeezing the rubber garden hose while you are spraying. This is where the first gain in efficiency lies.
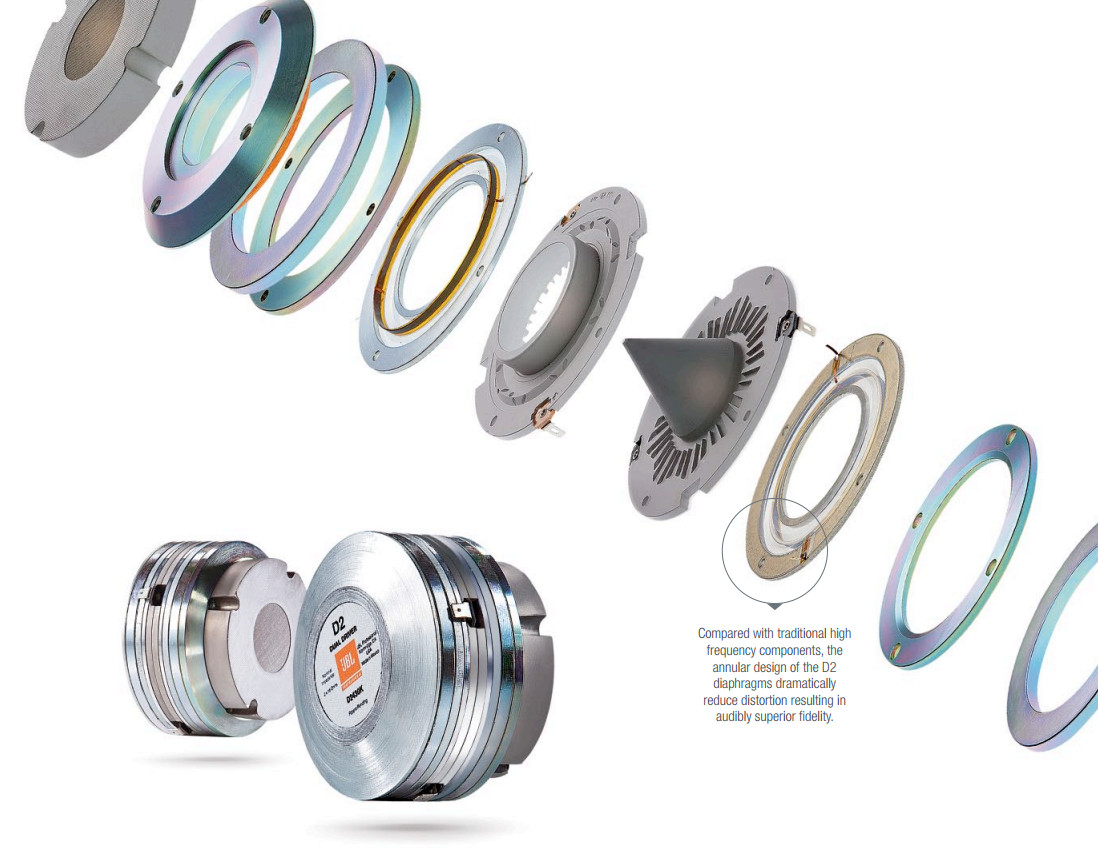
BL D2 Compression Driver Cross Section
JBL then couples the compression driver to a specially-shaped horn where the small-gap neck is coupled directly to the driver. The neck then extends to the mouth of the horn, which is considerably larger. The low radiation impedance of the source is thus much better matched to the high radiation impedance of the air, which again increases efficiency. It makes the combination of compression driver and horn extremely much more efficient than its traditional dome variant and just delivers 20dB more output with the same input signal. Nice if you want to provide the Gelredome with sound and still want to tap 100dB sound pressure at a distance of 50 meters.
JBL has been perfecting and refining this technique for years for home use. And now comes the trick – we don’t need that extreme sound pressure in our living room or cinema! To balance things out, the tweeter’s electrical input signal is attenuated so that it plays at the same level as its more inefficient companions, the midrange and woofer. And because the tweeter is so economical with the electrical power offered, very few watts go to the voice coil of the tweeter. They are all captured in the crossover filter of the speaker. The result: the electrical load is minimal, as is the diaphragm deflection and deformation. And that’s what JBL is all about. The dynamic and undistorted reproduction of the high tones without any form of stress.
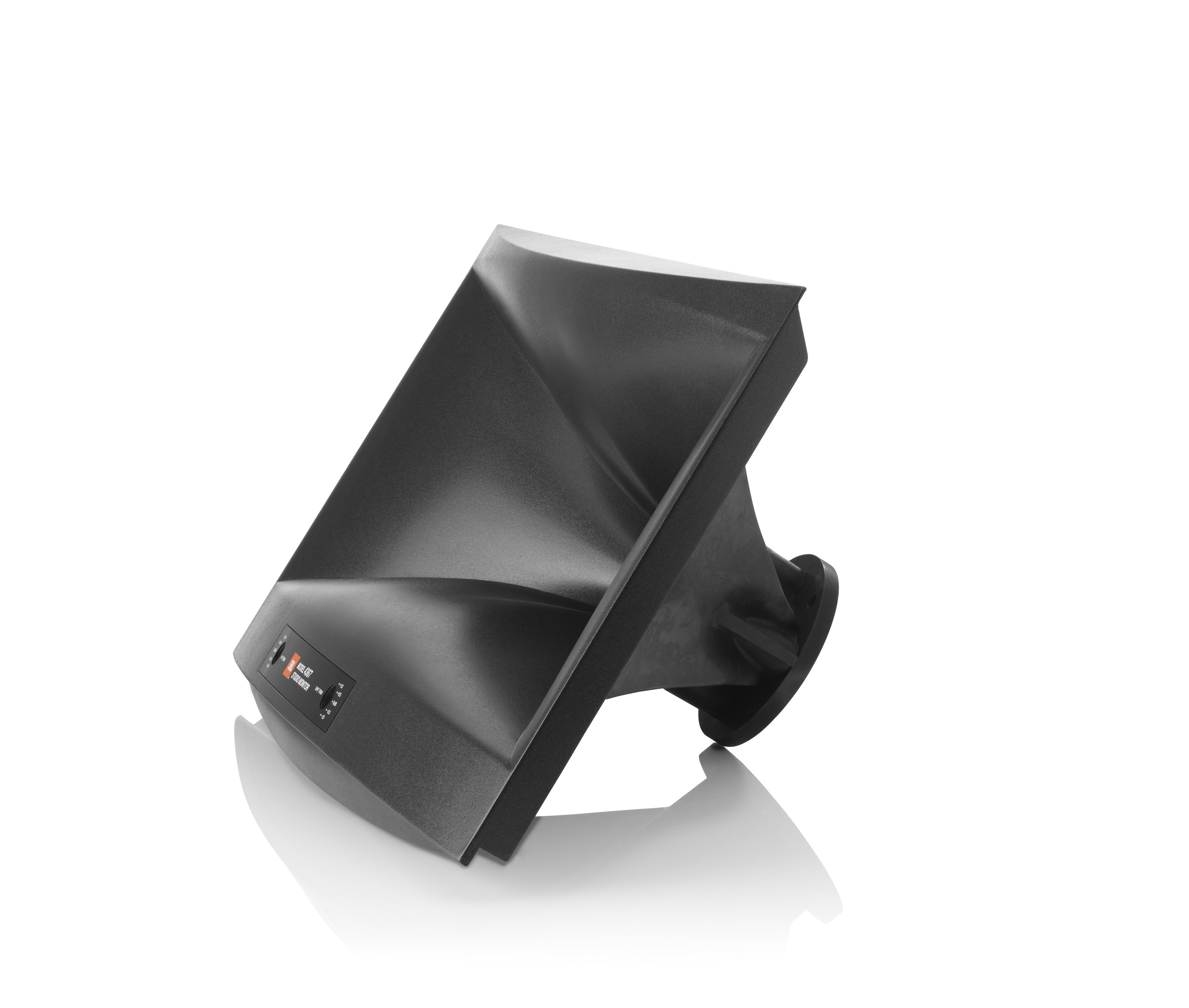
JBL HDI horn
And then the shape of that horn. Something in which JBL has been the absolute king for years. From the Shearer’s in the 1930s. Followed by the Folded-Plate Acoustic Lenses, the Dolly Parton’s and the Bi-Radial Horn’s to the HDI technology of today. Advancing insight fueled by ever-improving measurement techniques and research has shaped the horn systems into what they are today. There is a direct relationship between the shape of the horn and its radiation behaviour. Just like between the size and its working area. In addition, a horn is far from sacred. On the contrary, there are quite a few challenges associated with that technique and in all honesty there are also a lot of screaming bad guys among other designers. Among audiophile audiences, the horn is therefore not always equally lovingly appreciated. Mechanical resonances of the horn due to thin-walled construction, and along resonances along the length of the horn, can make certain tones sound louder than others. And that is of course not very pleasant. Not so with JBL.
The men have dubbed the last generation of horn High Definition Imaging Wave Guide. HDI for friends. The special aperture of the thick-walled horn skillfully directs the energy towards the listener, with the lobes in the mouth of the horn eliminating resonances. In addition, the radiation of the horn and therefore the tweeter fits much better with the radiation behavior of the woofer or midrange with which it must form a unit. The opening angle in which a JBL loudspeaker performs optimally balanced is therefore much larger than with a standard loudspeaker and where it starts to bundle, it does so in a much more controlled manner.
A JBL loudspeaker with compression driver and HDI horn sounds super energetic and dynamic. Compelling musical impulses or movie effects are reproduced extremely faithfully and with the greatest of ease. In addition, optimal sound can be enjoyed over a much larger seat. He follows dynamic jumps with 2 fingers in the nose. Without any stress or risk of overload. So it’s no wonder that JBL is the most popular brand for the Cinema and we tinkered with it in the Reference Sounds Experience Center 17 in our Cinema.
Whole story again. Brief summary? Come on then:
JBL Compression driver + HDI horn = Super efficient + high load capacity + large sweet spot
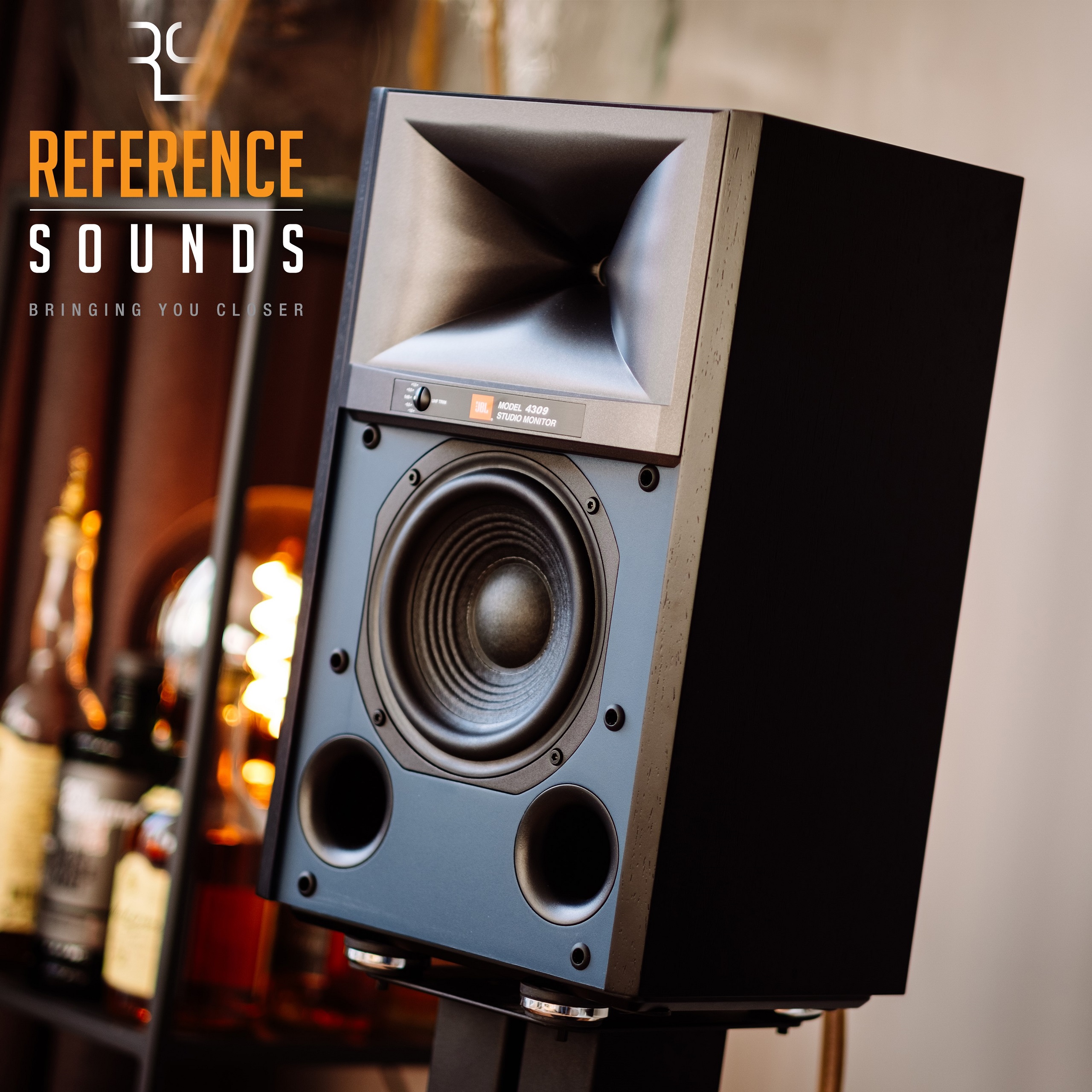